Deeside: Skills factory unveils new Industry 4.0 tech to train future generations of manufacturing workers
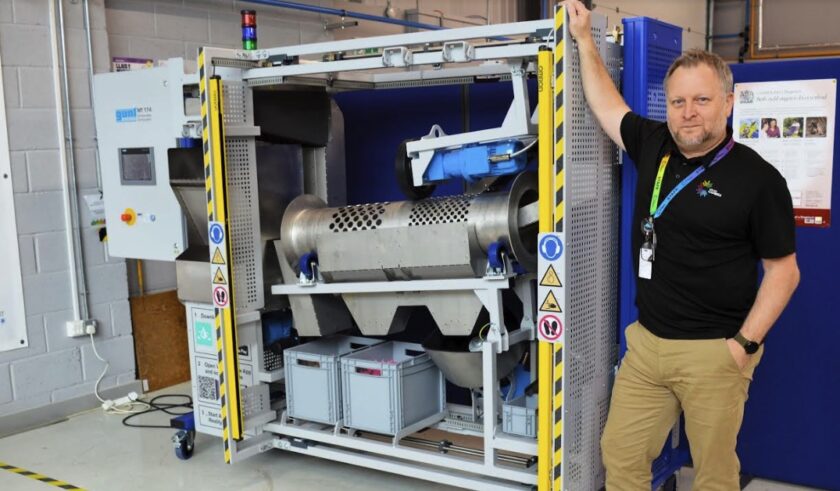
A skills factory unveiled groundbreaking new technology that will deliver cutting-edge Industry 4.0 training to students and manufacturing workers in North Wales.
Coleg Cambria has introduced a state-of-the-art industrial sorting plant and autonomous Universal Robot platform with ER Flex interface to its Deeside site.
The equipment was funded by Medru, a collaborative project between Cambria, Bangor University, and The Open University in Wales, supported by the Higher Education Funding Council for Wales (HEFCW).
Dan Jones, Curriculum Director for Advanced Engineering, said the machinery will be of value to students and those already working in industry, apprentices or time-served workers looking to upskill.
“The technology is incredible, and the sorting plant in particular will be pivotal in helping to educate groups of learners,” said Dan, from Prestatyn, who before turning to academia spent more than 20 years in the Armed Forces as a Military Control Systems Engineer prior to working as an Engineering Manager in local industry.
“The machine’s system is applicable to a wide range of themes from health and safety and industrial sensor technology to condition monitoring systems and maintenance and repairs.
“The scenarios that present themselves while working in a factory can be replicated here at the college, it’s a fantastic addition to our suite of equipment and a significant investment from Medru, so we are very grateful.”
The industrial sorting plant – built by Germany company, Gunt – can simulate many different outcomes and processes, dividing items by colour, size, material, weight, and other categories.
The plant is controlled via touch screen, and an operating mode and a training mode are available.
The training mode is used to simulate time- and sensor-controlled maintenance work and there is an augmented reality interface for mobile devices which offers extensive additional functions, such as the display of exploded views and data sheets.
The process uses an open design so that all components are freely accessible. Extensive safety equipment, such as light barriers in accessible danger areas, ensure safe operation. For the removal and installation of the gear units, the plant has a crane that can be set up in three different positions.
Users will further develop their hand skills, and Dan said they are able to create problems for learners to identify and solve, as they would have to in a real-time, real-world work setting.
“Fault-finding on automated systems is something which is often not trained, it is reactive and comes with experience, so being able to prepare maintenance teams to better anticipate any issues is a big USP,” he added.
“We are already getting a positive response in north east Wales and would like to collaborate with local businesses to test this machine further, so it can be tailored to any environment.
“Initially, our part-time learners will use it but eventually it will become a centrepiece for our Level 3 and Level 4 students in Advanced Manufacturing Engineering.
“We want the curriculum here to match what is happening out there in the sector, so our learners are ready for the world of work and have been trained using relevant technology on leaving college.
“We were already renowned for that, and with this addition to our facility it advances our position further in local industry.”
Medru aims to provide learners with the opportunity to achieve valuable Industry 4.0 technical skills and knowledge and deliver training across north east Wales, creating a pipeline of talent for the future.
Spotted something? Got a story? Email: [email protected]
Latest News